Greetings
Our job is to shape our customers thought.
Our company established since 1968, still continuously manufacturing products until now. In our company history various skills and technologies are packed in manufacture. We have continued to support with use of this skill and technologies as a gbacksideh from customers so they can manufactured better products. Our job is to shape our customers thought. From this onward we will continue to support as gbacksideh from our customer creation and would be delighted to continue shaping customers expectation.
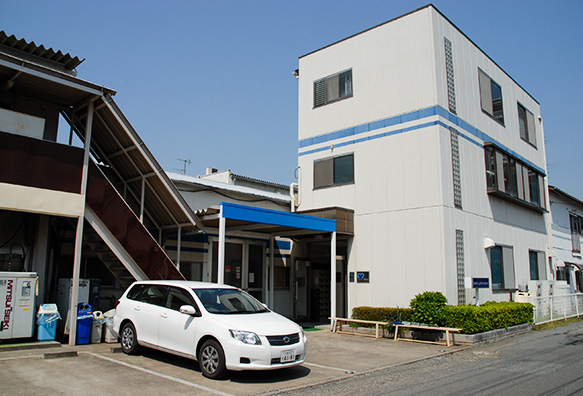
Company overview
Company name | Hokkai M.I.C Co.,Ltd |
---|---|
Capital | 30,000,000 JPY |
Establishment | August,1968 |
Executives | President Jun Abe |
Employee number | 30 people |
Average years | 42.7 years old |
Business Contents | Design, Manufacture and Sale of Powder Metallurgy Molds |
Head office / 1st factory |
Hokkai M.I.C Co., Ltd. 3-147 Nisshin-cho,Kita-ku, Saitama-shi ,Saitama
331-0823, Japan TEL : +81-48-665-6221 FAX : +81-48-651-0133 E-mail : csg@hokkaimic.co.jp |
2nd factory | 2-259-5 Yoshino-cho,Kita-ku, Saitama-shi ,Saitama 331-0811, Japan |
Homepage | http://www.hokkaimic.co.jp |
Email address | info@hokkaimic.co.jp |
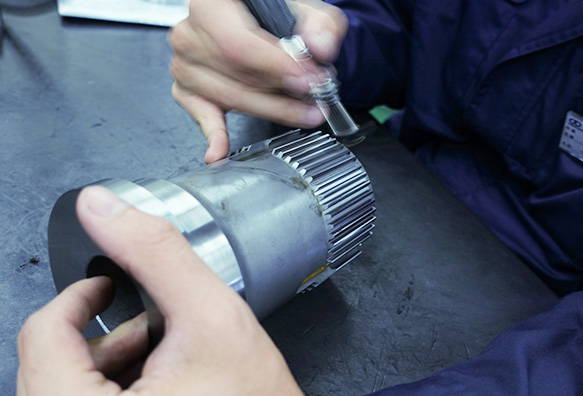
History of Our Company
- 1968
-
Established as Hokkai Metal Industry Co., Ltd.
with a capital of 5 million yen in Shinagawa-ku, Tokyo
- 1971
- Moved to Saitama city (former Omiya city) for business expansion.
- 1977
- Capital increased to 15 million yen.
- 1984
-
Saitama-shi (former Omiya-shi) Establishment of second factory in Yoshino-cho.
Received the Best Corporate Award from Saitama Prefecture.
Received designation of standard factory from Saitama prefecture.
Expansion of No. 2 factory.
- 1988
- Do capital investment of 130 million yen to enter the new field.
- 1990
- New office building completed.
- 1992
- Capital increased to 30 million yen.
- 1997
- Certified as gSAI NO KUNI Factoryhin Saitama Prefecture.
- 1999
-
On the occasion of its 30th anniversary,
Changed to HokkaiMIC Corporation.
Received Community Contributor Award from Medium and Small-size Company Excellence Management .
- 2000
- Developed order management system (OMS) in house.
- 2006
- Saitama-shi (former Omiya city) Establishment of third factory in Yoshino-cho.
- 2007
-
Change president
LMC is newly established to strengthen all processes.
- 2008
- Exhibited at Machine Element Technology Exhibition (Tokyo Big Sight)
- 2009
-
Exhibited at Machine Element Technology Exhibition (Tokyo Big Sight)
Factory integration.
Certified as Saitama City Technical brand company.
- 2010
-
New development department formed.
Exhibited at Machine Element Technology Exhibition.
Exhibited at motor technology exhibition.
- 2011
-
Exhibited at Open Machine Element Technology Exhibition.
Exhibited at motor technology exhibition.
- 2012
-
Exhibited dust core in EV exhibition.
Exhibited at battery exhibition.
Mass production test for mass production of dust core.
History of Technology
- 1968
-
Start production of cemented carbide.
Started making powder metallurgy mold.
- 1977
- Expansion of manufacturing equipments for high-precision powder metal molds.
- 1982
- Expansion of measuring machines for high accuracy of powder metal molds.
- 1984
-
Developed non-magnetic material of cemented carbide and expanded production of powder of powder metal mold for magnetic material.
Installation of NC machine at the 1st plant.
Cleared the former JISO system for gear powder metal molds.
- 1988
- Start production of powder metal mold for automobile parts.
- 1990
- Installation of CAD-CAM.
- 1995
- Production of injection mold for magnetic material started.
- 1997
-
Start production of precision molds for motor.
Start production of fine blanking mold.
- 2000
-
Started cutting of high hardness material by introducing Makino 3-axis V33 machining center.
Installation of 3D CADECAM
- 2001
-
Installation of linear motor driven carving electric discharge machine.
Installation of linear electric motor driven wire electric discharge machine.
- 2003
- Installation of linear electric motor driven wire electric discharge machine.
- 2004
-
Installation of MA200 robotic system for electric discharge machining.
Installation of multifunction machine Integrex 200 - IIIS.
- 2007
- Machining centerENC lathe installation.
- 2008
- Installation of NC forming grinding machine to increase demand for gear shape die
- 2009
- Installation of 100 ton press Machine.
- 2010
- Introduction of special equipment for manufacturing Ultra precision cutter at the 2nd plant.
- 2011
- Installation of CAD for designing MIM (metal injection molding).
- 2012
- Mass production test for mass production of dust core.
- 2016
- Installation of Makino 5-axis machining center.